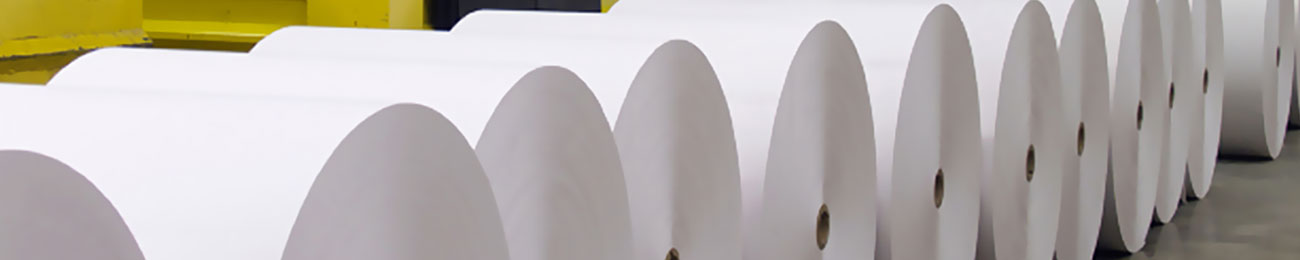
Bleaching
Bleaching traditionally has been achieved in industries, such as the pulp and paper industry, by the use of chlorine based agents. However, the use of these substances is coming under stricter guidelines, so alternative solutions are being applied.
Ozone is a powerful oxidant, even at low temperatures, meaning that it has a fast reaction time and effective bleaching propierties. It also allows for the elimination of acute toxicity and chlorophenolics, increasing the biodegradability of the effluent streams. The result of this procedure is twofold, with the first being the improvement to the environment and with it the improvement of regulation compliance.
The second is that ozone treatment makes it possible for the water quality to reach such a high level that it becomes possible to recycle it and reuse it, thus greatly reducing overall water usage in the process and making the treatment economically viable, as well as environmentally preferable.
Despite the advent of computers and electronic communication, demand for pulp and paper continues to rise worldwide. Given the high capital costs and inevitable drain on natural resources in this business, manufacturers are under strong pressure to maximize cost and process efficiency while reducing environmental impact wherever possible.
Oxygen can help to achieve these goals. It is indispensable in modern pulp manufacturing, where it is used, for example, in delignification, bleaching and ozone production. It can also help to increase capacity in the chemical recovery boiler or lime kiln. In addition, oxygen is useful in the forestry sector for wastewater treatment, in particular for odour removal and intensification of the activated sludge process.
Make Pulp Bleaching
Ozone is considered, from an ecological point of view, to be the best candidate for the bleaching of both hardwood and softwood pulp, in replacement for chlorine, in a combination-competition approach with other bleaching chemicals, such as chlorine dioxide, hydrogen Peroxide and per-Acetic Acid.
Ozone is used, either on high-consistency pulps (hc), containing 30 to 40% dry solids, or on medium-consistency pulp (mc), with 10 to 12% dry solids contents. In each case the process of mixing the gas with the pulp is the key factor.
HC Bleaching
The pulp is primarily acidified and pressed until a consistency of around 40%. A “drum” mixer is then used to optimize the contact of the gas with the pulp. In these cases, mixers operating at 2 bar are used.
MC Bleaching
The acidified pulp is directly treated in a mixer. In this case, mixing takes place at 12-13 bar. This assumes controlled compression without destroying the ozone. In both cases, the oxygen off-gases can be reused in the client’s process, either for oxygen delignification, oxidation of white liquor or for the waste water treatment stage, decreasing consequently the ozone variable cost.
Up to 25% saving combining O3 with CLO2 (Capex & OPEX)
Dissolving Pulp
As ozone is very efficient to control the viscosity, the chemical reactions with the pulp are not creating harmful compounds, ligno compounds produced in the cooking process are more easily removed with ozone inducing a cheaper process, ozone is a very good candidate for bleaching of pulps useful for textile.
Mechanical Pulp
Based on large scale pilot tests, use of ozone allows energy savings of more than 25%, while improving strength properties. Improved run ability on paper machines and better printing results on paper were noted (certainly in relation with the strong pitch removal effect of ozone).
Papermaking pulp bleached with OZONE totally chlorine free (TCF)
Since the end of the 80’s, much research has demonstrated that, with equally satisfactory results in terms of end product properties (whiteness, mechanical performances of fibers…), ozone could replace Cl 2, and possibly eliminate all chlorinated bleaching products using the OZP sequence that combines delignification using oxygen (O), ozone treatment (Z) and then hydrogen peroxyde (P) to produce a TCF paper. Furthermore, the use of Ozone for TCF papers, in combination with oxygen and hydrogen proxyde is much cheaper than without Ozone for the same final pulp properties.
Elementary chlorine free (ECF)
Even more economical, after oxygen delignification, only an ozone bleaching stage might be retained, followed by a wash – extraction under oxygen atmosphere and a final chlorine dioxide stage. This is the most cost-effective system and, consequently, the most widely used at present for ECF papers. The OZP line is also used to reduce chlorinated organic products discharge into the effluent by a factor of almost 10. this line also reduces discharged COD. Most of the bleaching sequences using Ozone are ECF combining Z and D stages.
OZONE Benefits
- Beneficial effects on the pulp
- Mechanical properties are not affected
- Optical properties improved
- Higher bulk, higher opacity of the paper
- Extractive content strongly reduced
- Yellowing is reduced, less brightness reversion
- Reduction of the water retention value
- Improved drainage, speed on the machine
- No formation of harmful by-products
- chromophore compounds
- Chlorate
- Dioxins, furans
- AOX in water effluents, OX in the pulp
Use of OZONE for treating effluents from pulp and paper industry
Pulp bleaching is the largest source of pollution in pulp mills waste waters. Suspended solids, COd, BOD, AOX and specific toxic compounds are generated. Pulp bleaching (especially when chlorine is used) produces most of these toxic substances. Ozone applied as a single treatment step downstream of a conventional biological treatment or combined with a complementary biological treatment can help to solve problems remaining after conventional Pulp & Paper waste water treatment plants.
- If just a polishing treatment is necessary to reach the residual color and COD guidelines, a single ozonation step can be the solution. typically ozone doses between 45 and 450 mg O3/l lead to 80% color removal and 20-25% cOd abatement.
- If hard COD downstream of the biological treatment is still high (> 350 mg/l) a solution is to implement downstream the main biological treatment an ozonation step followed by another biological treatment (preferably a Biological membrane reactor). Ozone doses can vary between 0.4 and 1 g O3/g COD.
- About 100 mg O3/l leads to about 40% of AOX abatement. A few hundred mg O3/l leads to about 50% of lipophilic wood extractives abatement and 90% of resin acids abatement.
- After ozonation of the effluent, acute toxicity and chronic toxicity decrease is generally observed.
- Finally, ozone can also be used against sludge bulking as well as for activated sludge reduction and improvement of their settleability and dewatering. The vents from the ozone reactors can be reused in the biological treatment.
Pulp bleaching : Specific technologies OZONE compression for MC-Bleaching
For mc bleaching processes the ozone gas coming from the ozone generator has to be compressed, usually from about 1 bar (g) to 10-12 bar (g), to the operating pressure of the mc-mixing equipment. OZONIA developed for this purpose a special ozone compression system to ensure unique compression efficiency by ensuring the highest reliability for P&P clients. the patented process is a combination of a NOx-scrubber with an appropriate liquid ring compressor. the scrubber is required to remove Nitrogen oxides which are produced in small concentrations inside the ozone generator. Nitrogen oxides form Nitric acids in the operating water of the compressor could result in very low ph-values. to stabilize the ph-value a special chemical is additionally dosed to the operating water. With the Ozonia compression system the ph value of the operating water is kept in the neutral range which consequently eliminates the risk of corrosion of the compressor.
The advantages of the OZONE can be summarized as follow:
- Gentle operation of ozone compressor
- no risk of corrosion caused by low ph-value
- No ozone loss caused by high pH-value in the operating water. High pH-value occurs at over dosage of caustic soda (conventional chemical used for stabilisation of ph-value)
- No ozone loss caused by diffusion of ozone in operating water. Dissolved Ozone is recovered by decompression of the water in the scrubber.
OZONE Destruction
The vent gas coming from the Z-stage usually still contains small amounts of ozone. Providing the off gas shall not be used for e.g. wastewater treatment, delignification, etc. the ozone in the off gas needs to be destroyed before discharging it to the atmosphere. The treatment of off gas needs special attention and know-how. In principle three ozone destruction methods are available.